The Paradigm Shift of Automation
In a Nutshell
Our customer was a manufacturing plant in a large multinational organisation. They recognised that to take the next step, efficiencies and product quality could only come with the consistency that automation provides. The challenge here was not technical. The challenge was to introduce a whole new way of doing things. We recognised that we needed to encourage our client to walk before they could run.
The solution was to implement a control system that was aligned with their budget and risk constraints. This meant that it was an entry level system, but like everything we do, was still robust. It also had the capacity to expand as they became more familiar with the price points and value of industrial automation, build the skills they required and witnessed the return on investment. That return is expected to fund further automation.
Our vision was to design a system for the future with all components suitable for a fully automated batch environment. We developed all equipment as control modules based on the S88 batch automation standard. We used simplified sequences in this initial application but these may later be changed in S88 phases.
Some Details
Seven mixing tanks with a physical IO count of around 150 points in three separate rooms were to be automated, a small automation project. The controller (PLC) selected was an Allen Bradley CompactLogix module with plenty of scope for future expansion or changes to IO configuration. The hurdle to overcome here was justifying the extended cost of replacing functional equipment like VSD’s.
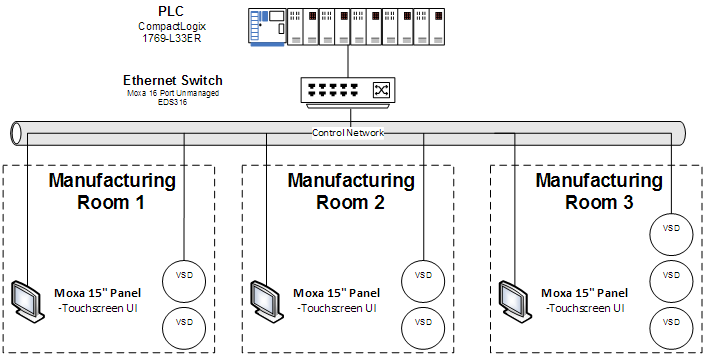
We selected Wonderware InTouch for the HMI software. This was installed on touch screen PCs for operation in the manufacturing rooms. One of our specialities is Wonderware’s ArchestrA platform. But in this case, the higher end system would be like using a sledgehammer on a thumbtack, an overkill for this stage of the journey. An engineering station was also omitted at this point.
Each HMI would default to the equipment in its own room but would have visibility of and provide control of any of the others. A natural redundancy was therefore created. The PLC controls the batching sequences, with a basic allowance made for 16 recipes. The operator makes recipe selections through the HMI. The flexibility for operational personnel to add more recipes themselves was also inherent in the design.
Physical intervention is still required but a fully automated batch system can only be implemented once automation of the manual process has fully taken place. The next expansion will include dedicated recipe management and batch reporting.
Cautiously selecting certain features to be implemented allowed us to minimise the software development costs which saw the ultimate ratios being:
Design | 11% |
Hardware | 65% |
Software | 24% |
The overall cost was more than the client was expecting but the cost per IO point was below typical price points. We plan to re-evaluate the value added in a year’s time which will allow us to help our other customers build better business cases of their own.
The end result: By automating their processes with an entry level system, we were able to modernise the business and help our client move to a more efficient working environment.